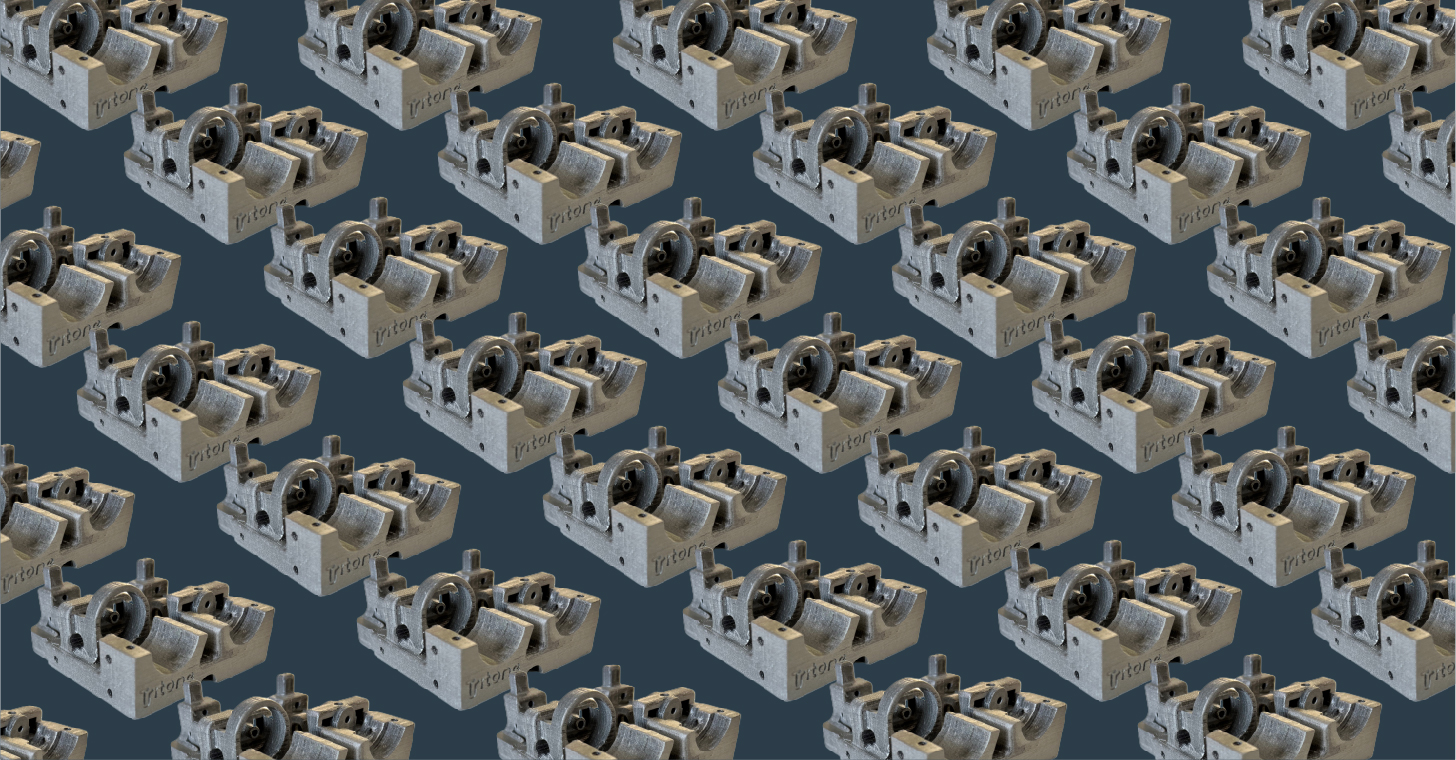
In the world of metal additive manufacturing, achieving repeatability is paramount for ensuring the quality and reliability of produced parts. Uniform results across multiple production runs are essential for many sectors demanding rigorous precision, such as aerospace, automotive, medical devices, defense, and more. However, this is easier said than done, as repeatability and consistency have long been pivotal challenges in metal additive manufacturing technologies.
This article will guide you through navigating repeatability challenges in metal additive manufacturing and introduce you to an innovative tool that addresses these challenges head-on.
Overcoming Repeatability Challenges with MoldJet’s Metal Additive Manufacturing Systems
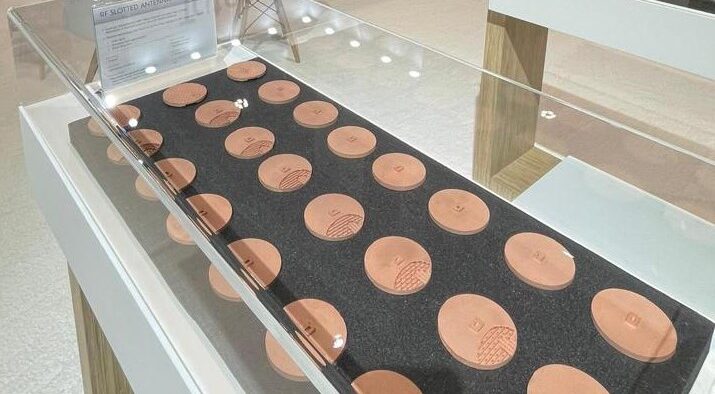
There have been significant strides in metal additive manufacturing technology, largely propelled by the development of the Binder Jet process.
With lower production costs and faster turnaround, the Binder Jet Process is promising. Yet, despite its advantages, this powder-based approach still struggles with inherent repeatability challenges that can significantly affect the outcome of the manufacturing process.
These challenges stem from two core assumptions of the Binder Jet Process: that micron-scale loose powder can be spread with perfect consistency and that jetted binders will infiltrate the powder bed uniformly. In practice, achieving such consistency is fraught with challenges due to the variability in powder properties and environmental conditions.
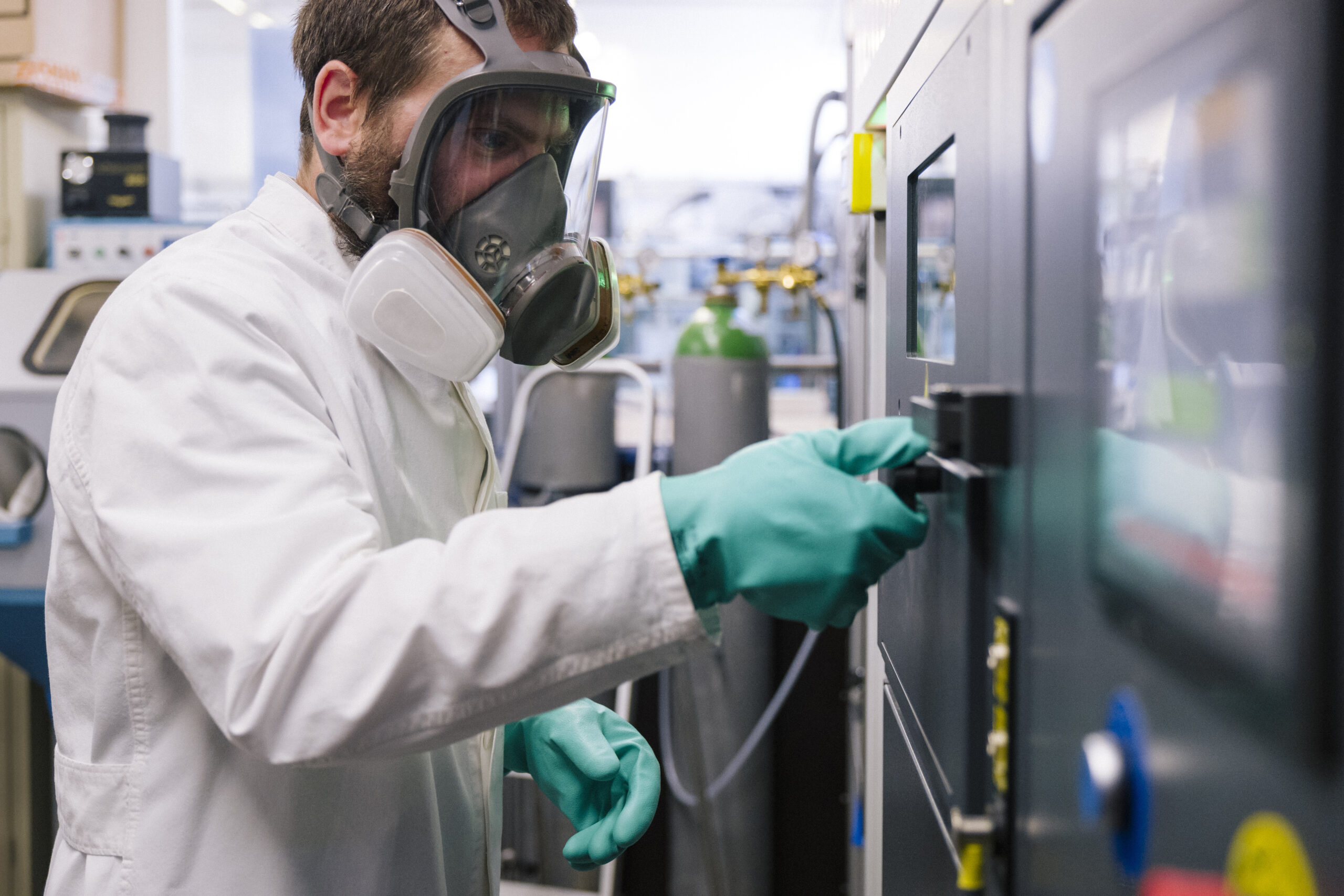
Impact of Environmental Conditions
Changes in humidity and surface chemistry significantly influence the spreading of powder and the infiltration of binders. The driving force behind binder infiltration is capillary action, which relies on the process of “wetting” or “saturation” of the powder by the binder. However, capillary forces make this process exceedingly difficult to control, introducing a significant level of variability. This variability can lead to inconsistencies in part densities and mechanical properties, not only between different build jobs but also within a single build job.
Variability in Saturation Rates
The rate at which the binder saturates the powder bed can fluctuate due to several factors, including the nature of the binder and the characteristics of the powder. This variability results in random density gradients within the printed parts, impacting their quality and dimensional accuracy.
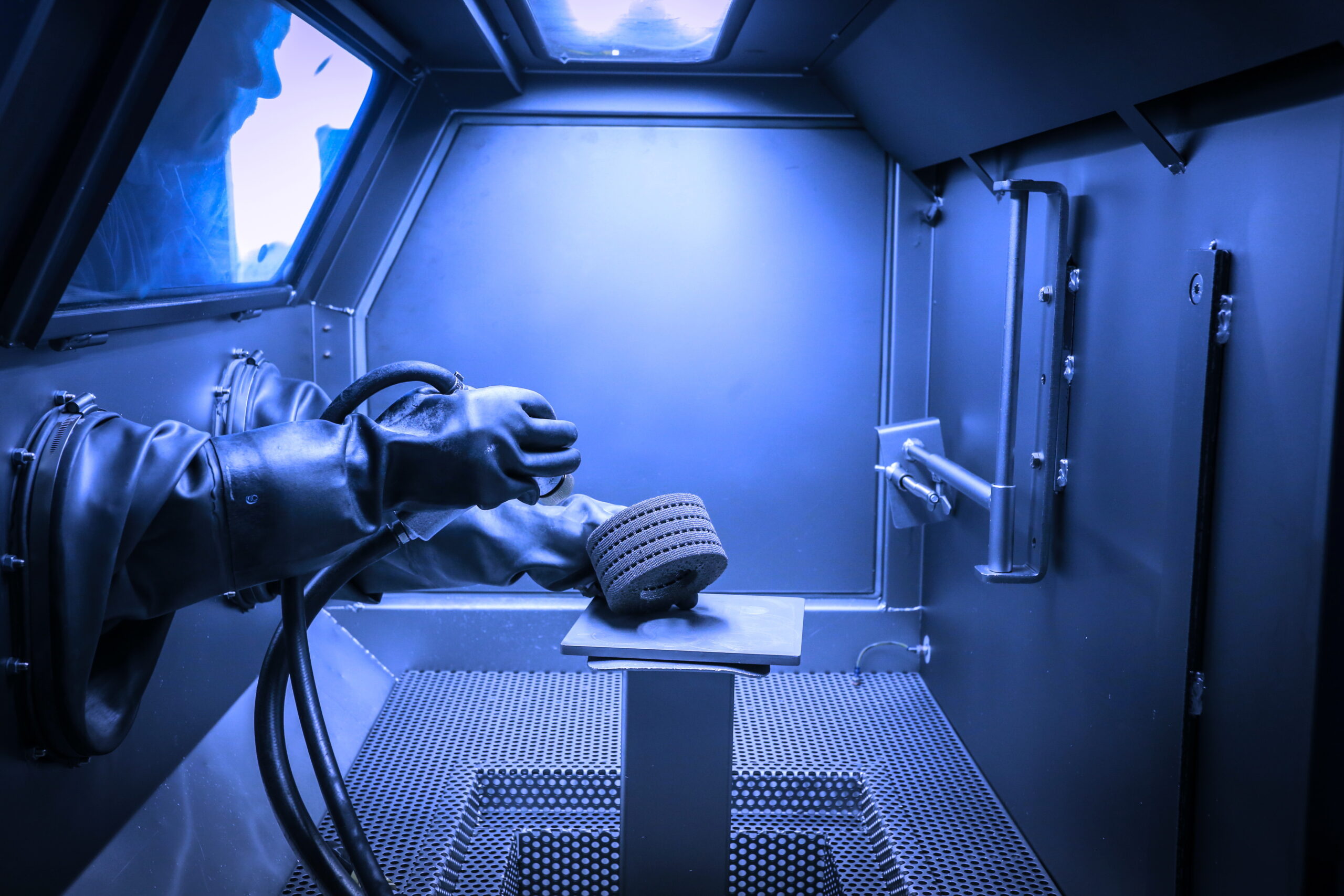
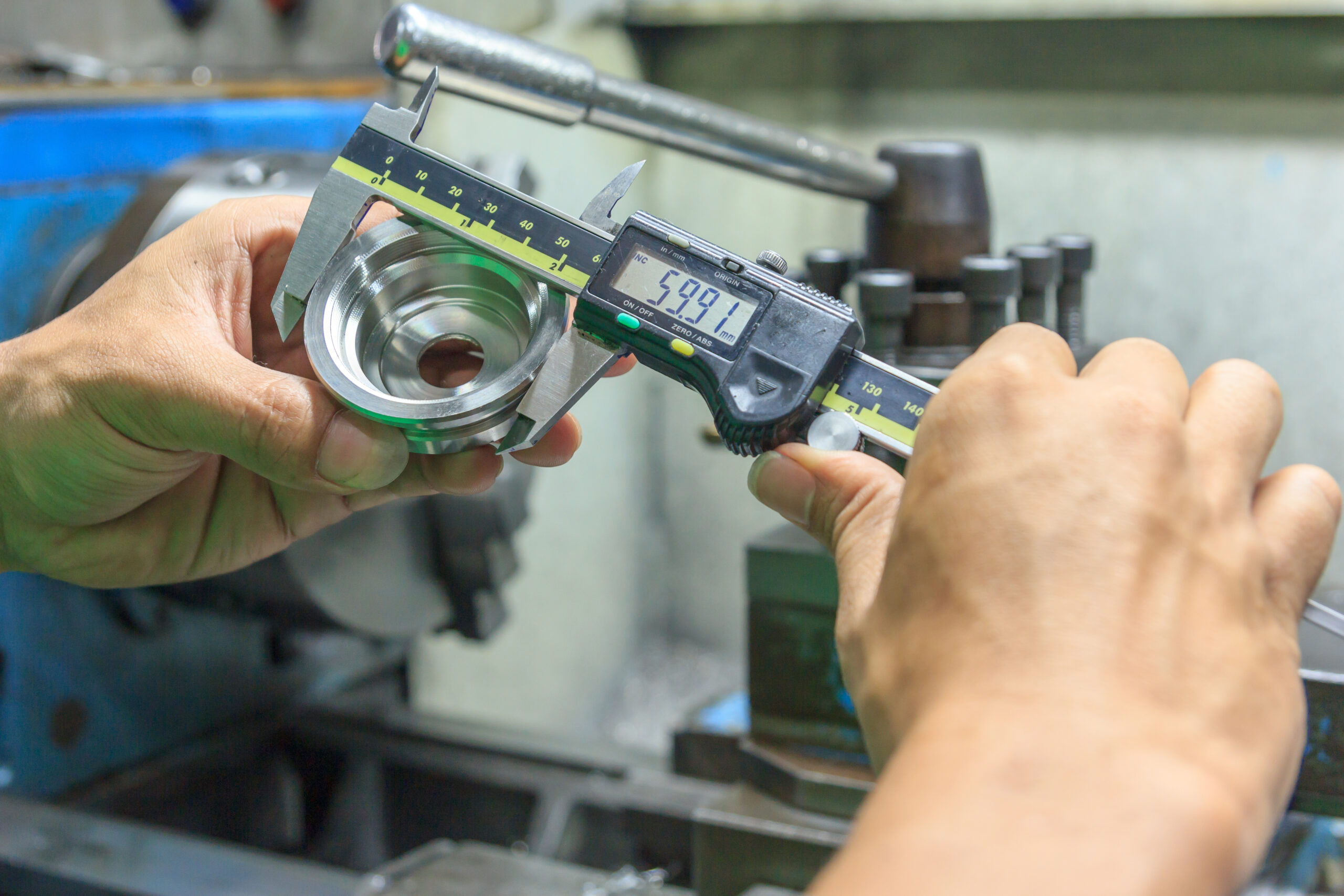
Localized Density Inconsistencies
The process of spreading loose powder, a fundamental step in the Binder Jet Process, can result in localized pack density inconsistencies, such as uneven layer thickness and compaction. These inconsistencies can be exacerbated by uneven wetting when binder droplets impact the powder bed, leading to further density gradients.
Challenges in Sintering
The non-uniformity in powder packing and binder wetting culminates in non-uniform shrink during the sintering process. Among plenty of other adverse effects, this results in poor dimensional tolerances and, ultimately, affects the usability and performance of the final parts.
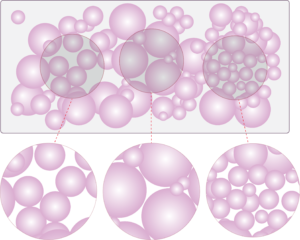
Given these substantial repeatability issues inherent in Binder Jet, the exploration of alternative sintering-based approaches may be worthwhile.
Overcoming Repeatability Challenges with MoldJet’s Metal Additive Manufacturing Systems
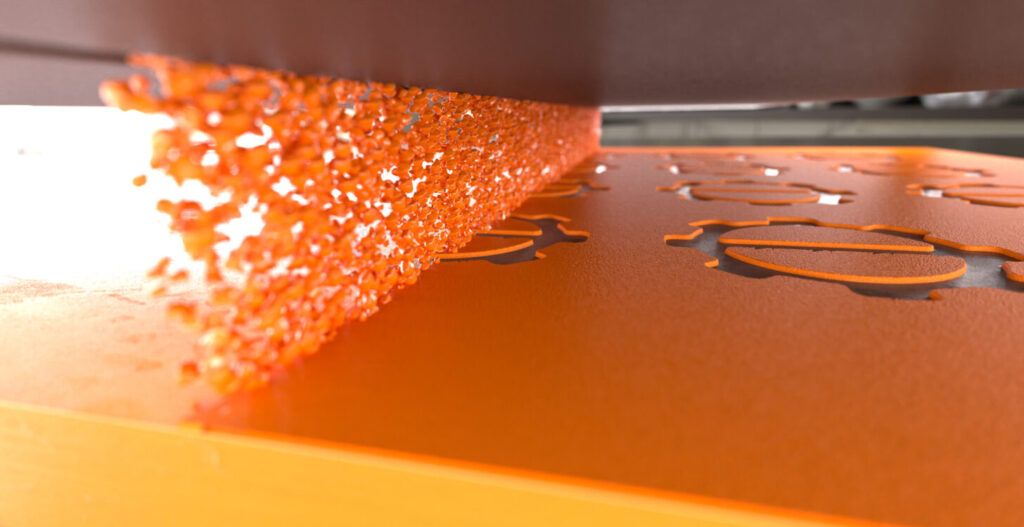
Tritone developed an alternative approach to Metal Additive Manufacturing that fundamentally differs from loose powder-based methods. MoldJet directly addresses and overcomes the repeatability challenges that have long plagued traditional powder-based methods like Binder Jet through several key innovations:
- Harnessing Inkjet Precision: At the core of MoldJet’s technology is the realization of inkjet technology’s full precision potential. By utilizing a wax-based mold material devoid of binders, the MoldJet system ensures the print head nozzles remain unclogged, enabling a stable and repeatable process. Unlike BinderJet technology, which requires adjustments in parameters based on the material or layer thickness, MoldJet operates with constant jetting parameters. This leads to a predictable and controlled phase transition upon the material’s impact on the build surface, in stark contrast to the unpredictable capillary infiltration process seen with the jetted binders in BinderJet systems.
- No Loose Powder: Unlike the Binder Jetting Process, which relies on spreading and layering fine metal powder, MoldJet technology uses a paste-based approach. MoldJet’s feedstock is not only premixed but also undergoes rigorous quality assurance checks at the materials plant before being supplied as a finished product. This guarantees uniform saturation of metal particles with binders, ensuring homogeneity from the outset. The simplicity of applying this mixture to the build-plate sidesteps the complications associated with powder-bed technologies, while continuous mixing maintains this uniformity throughout the printing process.
- Efficient Packing in the Build Layer: The subsequent step involves drying the wet feedstock within the build layer. This stage is pivotal as it transforms the metal particles from a slurry state, enabling them to align and compact in a highly orderly and efficient manner. The drying process ensures that the material particles are evenly distributed and densely packed, significantly enhancing the structural integrity and consistency of the printed object.
- Sintering Success: Sintering, a critical densification process, is significantly enhanced by starting with the highest possible density. MoldJet’s green bodies, characterized by their uniform and dense packing, require less densification and consequently experience less shrinkage during sintering. This minimizes adverse effects such as deformation, sagging, and cracking, addressing the primary sources of variation.
The Strategic Edge of MoldJet
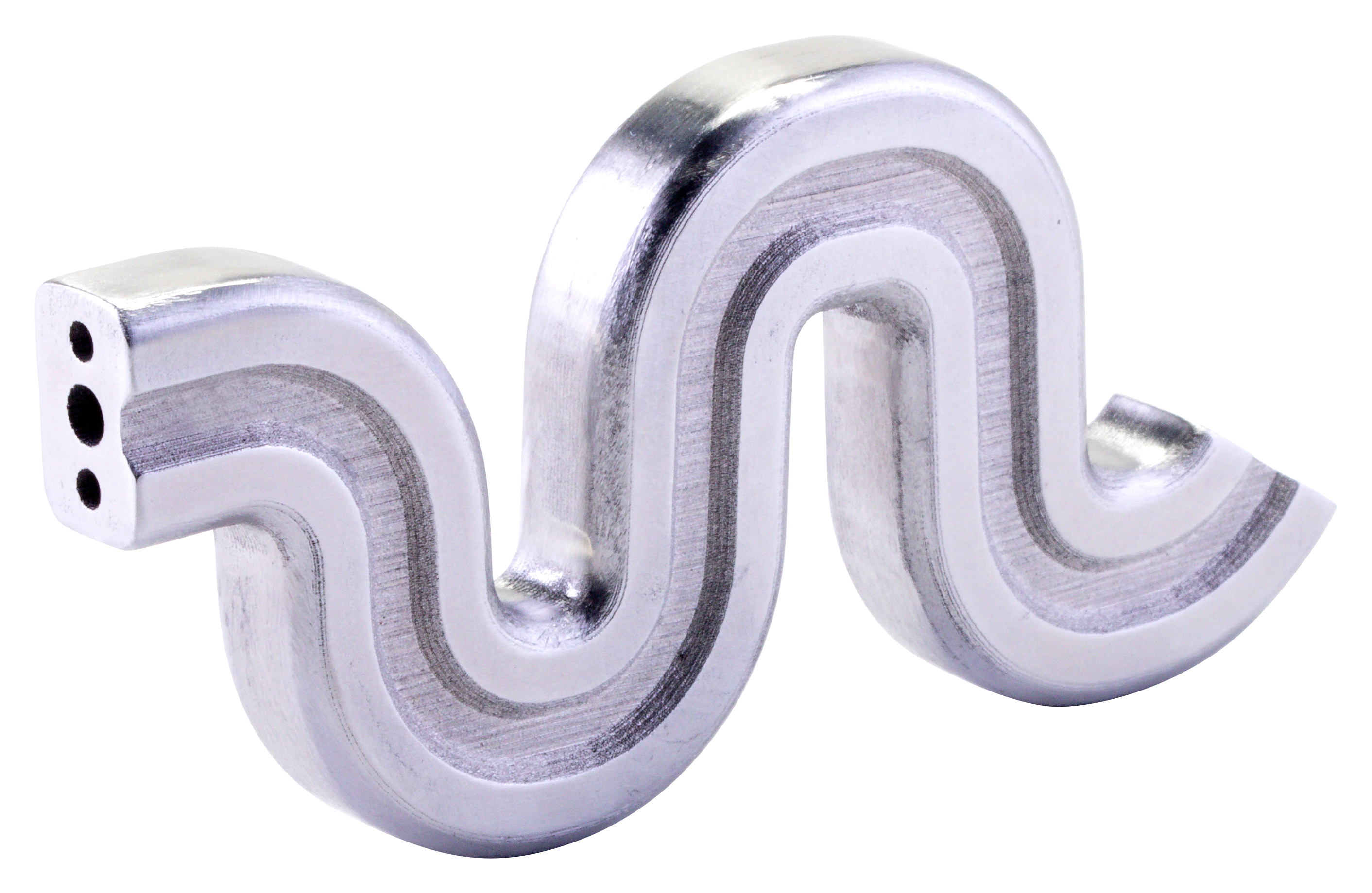
MoldJet technology not only addresses the repeatability challenges prevalent in the metal additive manufacturing industry but also introduces a suite of strategic advantages that transform the entire production landscape, from the initial design phase right through to the final product, offering businesses a significant competitive edge.
MoldJet’s paste-based approach notably revolutionizes the post-processing stage, greatly eliminating the removal of support structures and diminishing the need for extensive finishing work. This efficiency significantly reduces the variability often encountered in the final stages of manufacturing. Consequently, MoldJet facilitates a more efficient transition from printing to the final product, saving both time and costs.
Moreover, MoldJet’s ability to bypass the extensive post-processing usually required in metal additive manufacturing processes accelerates the production timeline without sacrificing part quality. This efficiency renders MoldJet particularly attractive for industries that demand rapid production cycles in conjunction with high levels of part precision and reliability.
One of the most distinguishing features of MoldJet is its versatility. Far from being a rigid, one-size-fits-all solution, MoldJet’s technology is highly adaptable and designed to meet the unique needs of a wide array of applications. Whether the focus is on creating small complex parts, larger bulky parts, easily changing materials between production runs, or utilizing materials that require high strength, MoldJet ensures the production of parts that meet the stringent quality standards of diverse industries.
A New Standard in Metal Additive Manufacturing
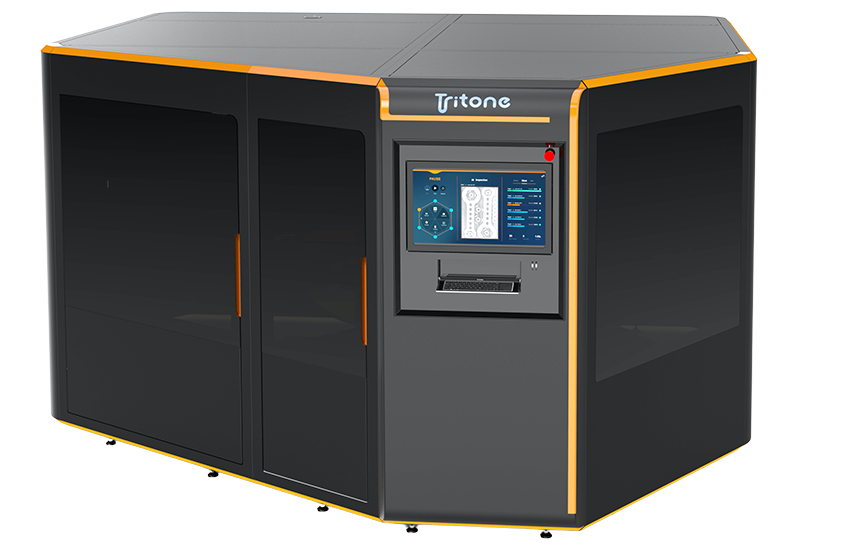
By tackling the inherent repeatability challenges of metal AM head-on, MoldJet sets a new industry standard, enabling the production of consistent, high-quality parts at scale. This opens up unprecedented opportunities for sectors where precision and reliability are paramount. MoldJet is at the forefront of redefining metal additive manufacturing, empowering our clients to harness the full potential of AM technologies for their critical manufacturing objectives.
Interested in learning how MoldJet can revolutionize your metal additive manufacturing needs? Contact Tritone to schedule a consultation and streamline your manufacturing process today.