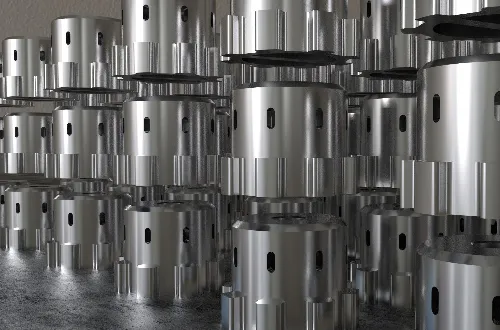
The world of metal manufacturing has been undergoing a significant transformation lately, affecting industries across the board, from automobiles to fashion to healthcare. No matter where you find yourself, the era of traditional manufacturing is rapidly evolving.
We are entering a new age driven by changing consumer preferences, evolving product requirements, shifts in economic landscapes, and dynamic shifts in supply chain dynamics.
Traditional manufacturing technologies are generally optimized for high-volume operations and are plagued by inefficiencies, material waste, and complexity when lower quantities or special runs are needed.
But here’s the exciting news: the future has arrived in the form of additive manufacturing, also called 3D Printing. This technology brings innovative and efficient methods to augment traditional manufacturing built around casting, machining, or stamping. While not a new concept, Additive technologies have evolved significantly in productivity and cost.. They are now transforming operations around the world.
So, let’s embark on a journey into the future of metal manufacturing, specifically the power of additive manufacturing and how this widely accepted innovation can elevate your operations ahead of your competition.
A Leap Forward in Metal Additive Manufacturing
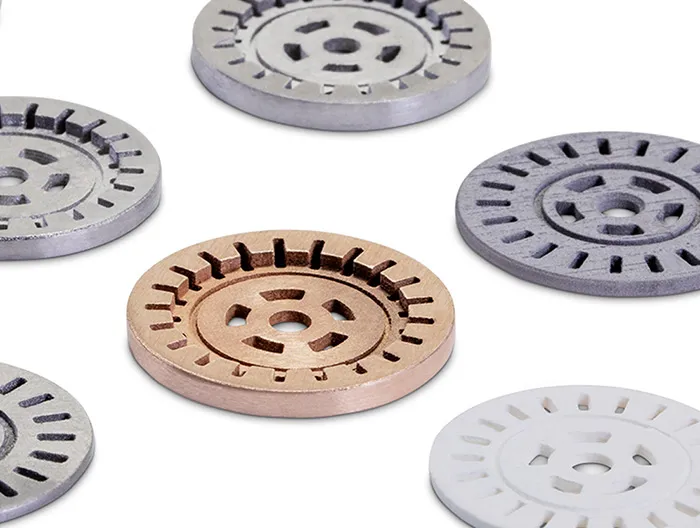
While many people think AM is limited in materials, the situation is changing… more metals every year.
There is already a long list of metals being used, including stainless steel, copper, super alloys, ceramic, and others. That list is continually growing, creating even more possibilities for metal manufacturers. Plus, with technologies like MoldJet, it is now easy to quickly change from one metal to another, enhancing the capabilities and possibilities of additive metal manufacturing even further.
Our MoldJet technology represents a significant leap in the realm of additive manufacturing. Our innovative, powder-free method is not just an incremental improvement; it’s a transformational approach that is reshaping the landscape of metal and ceramic part production. By eliminating loose powder from the process Tritone has made technology adoption easier and safer.
Enhanced Mechanical Properties
In addition to having options with metals and more access to short-run products, additives also play a role in saving time and reducing costs.
Avoiding large upfront tooling costs is a key cost saver as is reducing waste. Since metals are layered on, there is no need to machine off and discard large amounts of material. This leads to a more efficient use of raw materials.
As a result, smaller amounts of raw materials need to be purchased and almost none of it is wasted – as long as you know your specific needs for the project. Also, our MoldJet technology can change from one material to another quickly, meaning the entire process is more efficient with less downtime, allowing metal manufacturers to save both time and money.
Sustainability and Efficiency in Manufacturing
One byproduct of reducing waste is creating better sustainability in metal manufacturing. While this has always been a goal for the industry, additive have helped companies reach sustainability goals. As mentioned, fewer raw materials are needed and those that are used are placed with great precision. This means that almost nothing goes to waste.
With more efficient techniques, the amount of energy being used in production can also be reduced as much as possible. Of course, the metal manufacturing industry has always been cognizant of ways to recycle materials. With the growth of additive techniques on top of that, the future of metal manufacturing promises to be as smart and sustainable as ever before.
Complex Geometries and Advanced Metal Design
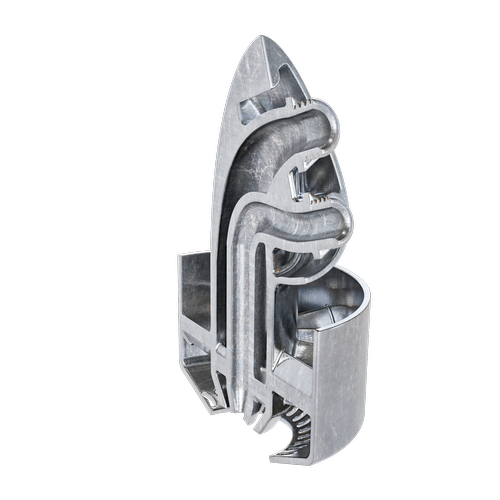
As mentioned, the capabilities of what metal manufacturers can do with additive and new technology are far greater. For example, our MoldJet technology is designed to create high-density, complex geometry parts. Therefore, more complex designs have become realistic without significantly higher costs.
The Precision Revolution: Our Layer-by-Layer Build Process
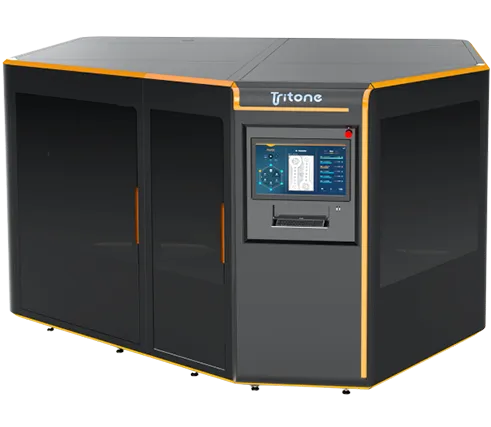
Additive manufacturing thrives on productivity and precision, and MoldJet technology is pushing these elements with its layer-by-layer build process.
This process begins with precise jetting to create mold forms, forming cavities that perfectly replicate the desired geometry for each layer.
Next, a high-density paste is carefully deposited into these cavities. The layer is then swiftly dried and hardened using a combination of hot air and vacuum, ensuring both structural integrity and speed.
This process repeats layer by layer.
Post-production involves hands-free demolding, followed by a single-step thermal debinding and sintering process. This streamlined approach not only enhances manufacturing efficiency but also results in robust, low-shrinkage parts, making our system exceptionally efficient. The drying and hardening stage follows swiftly, thanks to the precise application of hot air and vacuum, facilitating the rapid transformation of each layer into a solid, robust structure. This reduction in production time comes without any compromise on quality.
Embracing the Future of Metal AM
As you continue to navigate through the ever-changing world of metal manufacturing, our MoldJet Technology has your back. It not only addresses the limitations of traditional approaches but propels manufacturing into an era of unparalleled potential.
The ability to create high-density, complex geometry parts with a wide variety of materials opens doors to creative designs and functional solutions that were once out of reach. No matter your industry, your creation is our command. Our technology promises to redefine the very essence of your manufacturing process.
Governance Commitment
Additive manufacturing is revolutionizing many aspects of the automotive industry from new product development to robust “on demand” spare part production. As companies explore ways to integrate this technology, key attributes are equipment flexibility, ease of use and safety. Tritone’s MoldJet process checks all these boxes. Our Powder Free approach makes it safe and easy to explore a wide range of materials and then scale production as applications gain traction and volume grows.
Ready to experience unmatched quality and efficiency for yourself: Visit our website now to check out our innovative product and take your manufacturing to the next level. Don’t miss out – explore Tritone today!