In today’s rapidly evolving manufacturing landscape, the demand for unique metal parts with complex geometries is higher than ever. However, producing such intricate designs, particularly those with internal features like tunnels and holes, presents significant challenges for additive manufacturing (AM) technologies.
Challenges in Achieving Complex Geometries
Additive manufacturing technologies, while innovative, encounter several obstacles when tasked with producing parts that require advanced internal features:
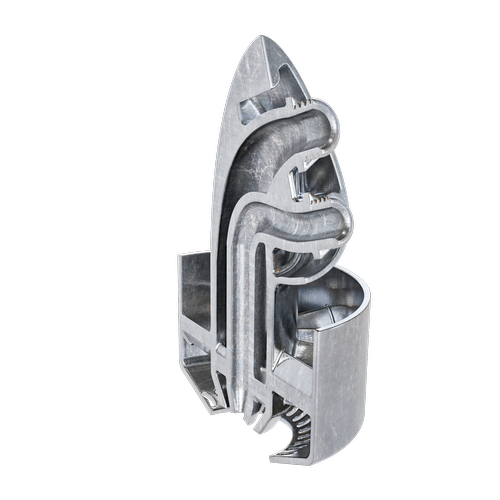
- Material Limitations: Many AM processes are constrained by the types of materials they can use. Some materials may not flow well enough to fill intricate internal designs, leading to incomplete features or structural weaknesses.
- Support Structures: Complex geometries often necessitate the use of support structures to prevent deformation during the printing process. These supports can complicate the design and add to post-processing time and costs, particularly when they obstruct internal features.
- Thermal Management: Parts with internal tunnels may face issues related to thermal expansion and contraction during the printing process. Uneven heating can lead to warping or cracking, making it difficult to maintain dimensional accuracy.
- Surface Finish: Achieving a smooth surface finish on internal features is challenging. Many AM technologies require extensive post-processing to achieve the desired quality, which can negate the time and cost savings typically associated with additive manufacturing.
- Design Complexity: The intricacy of internal features often demands advanced design and engineering expertise. Optimizing these designs for manufacturability while ensuring they meet performance requirements can be a daunting task.
Given these challenges, manufacturers need a solution that not only addresses these issues but also enhances the efficiency and effectiveness of the production process. This is where MoldJet technology comes into play, offering a groundbreaking approach that simplifies the creation of complex geometries while maintaining high quality and performance.
MoldJet Technology: A Solution to Internal Features
Moldjet technology emerges as a groundbreaking solution to the challenges associated with producing complex geometries. This innovative process is designed specifically for high-throughput production of metal and ceramic parts, enabling the creation of intricate designs with exceptional mechanical properties.
How MoldJet Technology Works
MoldJet technology operates through a series of well-defined steps that allow for the efficient production of parts with complex internal features:
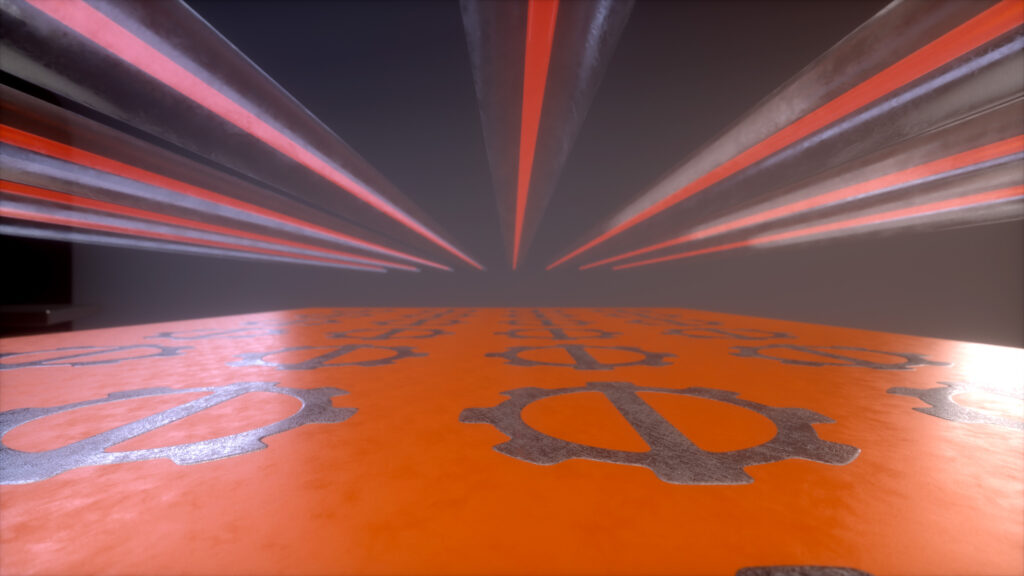
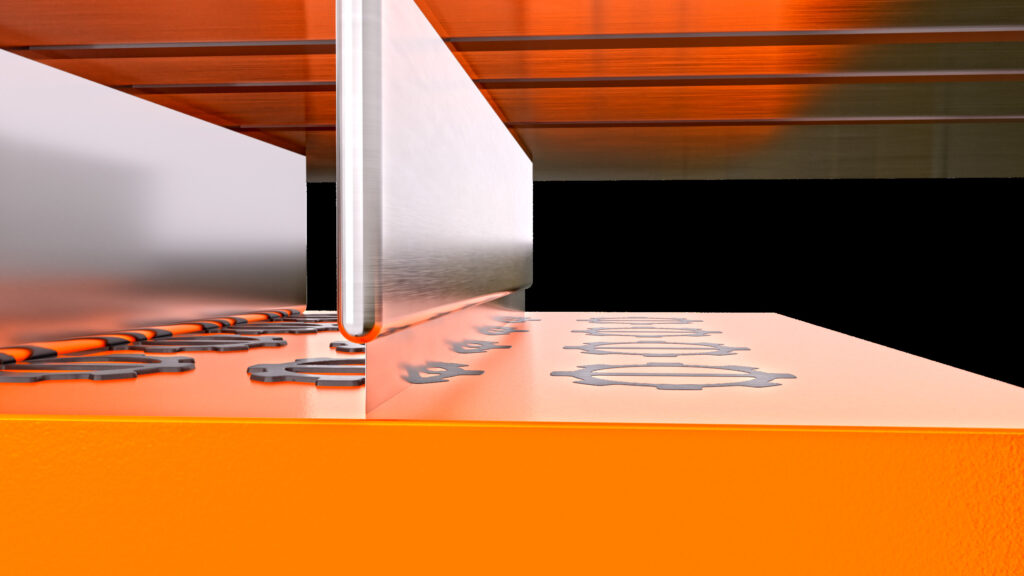
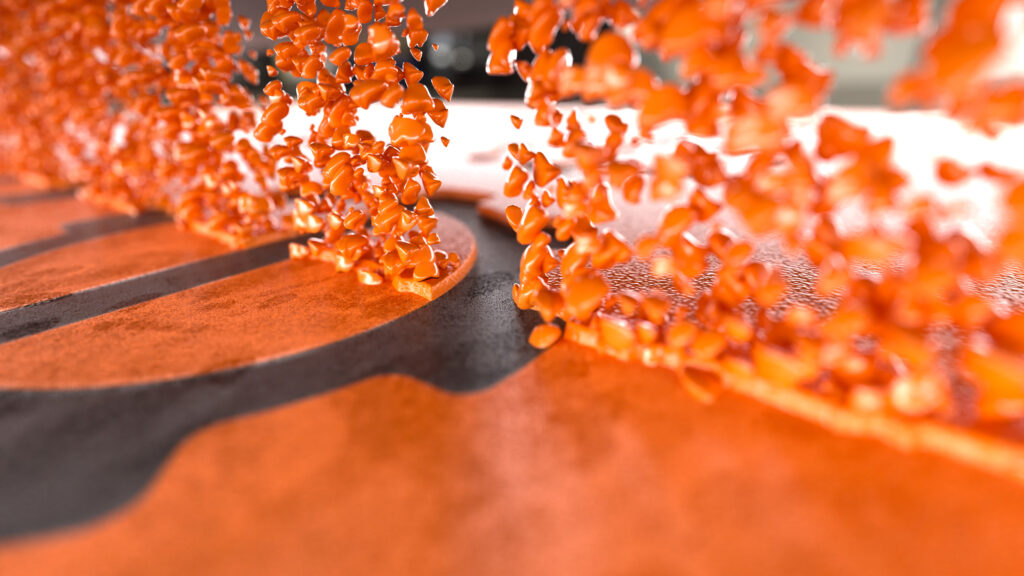
- Mold Layer Creation: The process begins with the jetting of mold material to form the cavities that mirror the desired part’s geometry. This layer-by-layer approach allows for the creation of highly detailed internal structures.
- Filling with High-Density Paste: A specialized high-density paste is then injected into the mold cavities, ensuring that every detail of the internal features is accurately captured.
- Drying and Hardening: The filled molds are rapidly dried and hardened using hot air and vacuum, preparing them for the next phases of production.
- Quality Assurance: Real-time AI image analysis is employed to monitor the process, ensuring that any deviations from the intended design are corrected immediately.
- Demolding Process: Once the parts are formed, the mold material is removed through a hands-free melting process, revealing the green parts, which are then rinsed to prepare for sintering.
- Final Processing: The green parts undergo thermal debinding and sintering in a single stage, transforming them into fully functional metal or ceramic components.
The standout feature of MoldJet technology is its ability to produce parts with complex internal geometries without the need for extensive post-processing. This capability not only enhances design freedom but also significantly reduces lead times and manufacturing costs.
Conclusion
As the demand for intricate metal parts continues to grow, overcoming the challenges associated with producing complex geometries becomes imperative. MoldJet technology represents a significant advancement in additive manufacturing, providing a streamlined process that enables the creation of unique designs with internal features. By embracing this innovative technology, manufacturers can unlock new possibilities in metal part design and production, ultimately driving efficiency and performance in their operations.