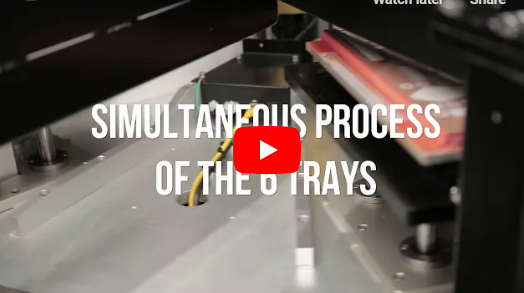
Imagine a world where intricate designs are brought to life with ease, where innovation isn’t stifled by costly tooling, and where spare parts are available on-demand, eliminating crippling downtime. That world is here, thanks to the transformative power of metal 3D printing!
Across industries, the demand for sophisticated mechanical systems that perform targeted tasks is ever-increasing. These systems require meticulous design, rigorous development, and unwavering reliability. But the traditional path to creating these assemblies is fraught with challenges: the high cost of custom parts, lengthy lead times, and the constant need for readily available spare parts.
For years, machine designers have grappled with the trade-off between using readily available, off-the-shelf components and creating custom parts tailored for optimal performance. The problem? Custom parts often require expensive CNC machining or casting, especially when dealing with the low volumes typical in specialized machinery.
This creates a bottleneck, hindering innovation and extending product development cycles. And when equipment breaks down in the field, the need for replacement parts becomes urgent, forcing companies to invest in costly warehousing and endure frustrating delays.
Enter Metal 3D Printing
a resolution that’s rewriting the rules of manufacturing. By building parts layer-by-layer from a digital design, metal 3D printing eliminates the need for expensive tooling and fixturing. This unlocks a world of possibilities:
On-Demand Spare Parts: Eliminate warehousing costs and minimize downtime by printing the parts you need, when you need them.
Unleash Design Freedom: Imagine creating parts with complex geometries, internal cooling channels, and optimized designs that were previously impossible to manufacture.
Consolidate Assemblies: Reduce complexity and improve reliability by combining multiple parts into a single, multi-functional component.
Test and iterate designs rapidly without the burden of tooling costs, accelerating your time to market.
slash production costs and lead times
3D metal printing empowers businesses to create complex parts on-demand and revolutionize their manufacturing processes for a faster, more efficient future. It’s not just about printing parts; it’s about printing progress.
Real-World Impact:
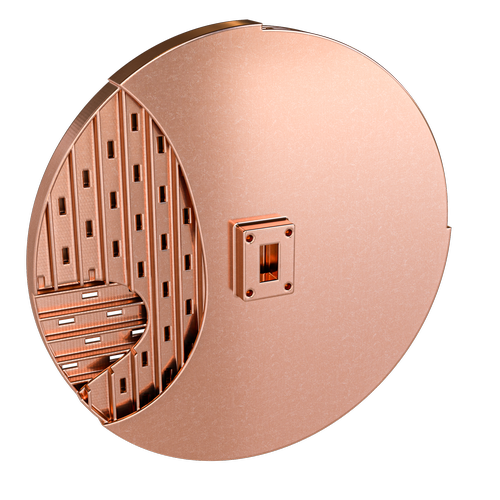
- A diffuser, traditionally made from many separate parts, can now be 3D printed as a single, unified component.
- A Bevel gear can be rapidly tested, avoiding the costly investment in casting Molds for each iteration.
- An RF Slotted Antenna with complex geometries can be printed on-demand, eliminating the need for large inventories.
Metal 3D printing isn’t just a technology; it’s a catalyst for innovation, efficiency, and resilience. It’s empowering companies to break free from the constraints of traditional manufacturing and create a future where anything is possible.
Interested in learning how MoldJet can revolutionize your metal additive manufacturing needs? Contact Tritone to schedule a consultation and streamline your manufacturing process today.