Exceptional industrial serial manufacturing
High manufacturing resolution and precision enable complex part geometries
Address demanding market requirements
Uniform, repeatable manufacturing with high density and accuracy of parts
A green and safe industrial environment
A powder-free process and hands-free post process, enabled by a paste-based feedstock
Developed for Mass Production
Tritone revolutionizes metal Additive Manufacturing to meet the high standards of industrial production.
Our innovative technology empowers efficient production of precise parts in various metals and ceramics, serving industries such as Automotive, Aerospace, Medical, and Consumer Electronics.
Our benefits
Discover enhanced efficiency and simplified tasks with our solutions. Our technology boosts productivity, achieving more in less time. Elevate your professional image with precision-focused solutions.
Explore a variety of opportunities as we help you and your customers open new categories, markets, and industries. With our innovative solutions, you can expand your reach and tap into previously unexplored areas.
Eliminate loose powder, reduce setup time, and optimize the density of green parts to enhance your bottom line. By minimizing waste and streamlining processes, our solutions drive efficiency and profitability, ensuring a more cost-effective operation.
our manufacturing systems
dominant
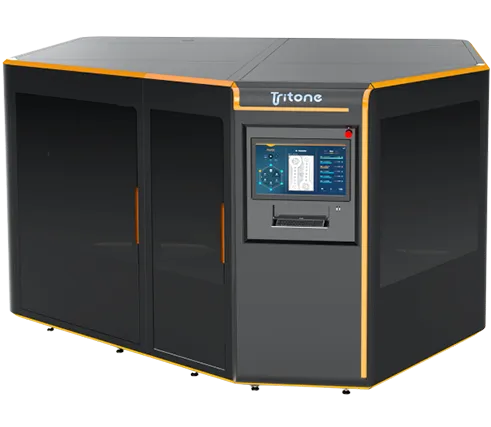
- Number of trays: 6,
simultaneous and independent - Throughput: Up to 1,600 cc/h
- Total build volume: 70,000 cc
Dim
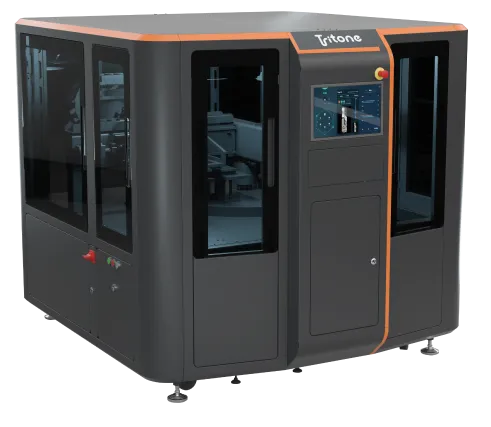
- Number of trays: 4,
simultaneous and independent - Throughput: 220 cc/h
- Total build volume: 10,000 cc